Position Statement
Commentary
6.1 Definitions
6.1.1 Waterproof – An idealized property of a material indicating imperviousness to water in either liquid or vapor state. (See also Dampproofing.) Note: because nothing can be completely impervious to water under infinite pressure over infinite time, this term should not be used.
“CT-18 ACI Concrete Terminology”, American Concrete Institute, Farmington Hills, MI, 2018
6.1.2 Concrete Surface Profile (CSP) – The topographic contour of the exposed surface of a material or substrate.
“310.2R-2013 Selecting and Specifying Concrete Surface Preparation for Sealers, Coatings, Polymer Overlays, and Concrete Repair”, International Concrete Repair Institute (ICRI), St. Paul, MN 2013
6.1.3 Dampproofing – treatment of concrete or mortar to retard the passage or absorption of water or water vapor either by application of a suitable coating to exposed surfaces, or by the use of a suitable admixture or treated cement, or by use of a preformed film such as polyethylene sheets placed on ground before placing a slab. (See also Vapor Retarder.)
“CT-18 ACI Concrete Terminology”, American Concrete Institute, Farmington Hills, MI, 2018
6.1.4 Dampproofing System – A single product or series of compatible products designed to dampproof a structure.
The system may be comprised of products from one or more manufacturers.
6.1.5 Dampproofing Type – Currently there are four common types of dampproofing used in the watershaping industry:
- Protectants and Treatments (see 6.4.1)
- Rigid Cementitious (see 6.5.1)
- Fluid Applied Elastomeric (see 6.6.1)
- Highly Modified Cementitious (see 6.7.1)
6.1.6 Efflorescence – A generally white deposit formed when water-soluble compounds emerge in solution from concrete, masonry, or plaster substrates and precipitate by reaction such as carbonation or crystallize by evaporation.
“CT-18 ACI Concrete Terminology”, American Concrete Institute, Farmington Hills, MI, 2018
6.1.7 Exposure Class – Designation used to describe environmental conditions to which concrete will be exposed.
“CT-18 ACI Concrete Terminology”, American Concrete Institute, Farmington Hills, MI, 2018
6.1.8 fc’ – Specified compressive strength of concrete, psi.
“ACI-318 Building Code Requirements for Reinforced Concrete”, Chapter 2 Definitions, American Concrete Institute, Farmington Hills, MI
6.1.9 Impervious – Describes a material having a % absorption of water by weight less than or equal to 0.5%. Impervious materials are suitable for interior, exterior, and submerged locations.
“ASTM C97-18 Standard Test Methods for Absorption and Bulk Specific Gravity of Dimension Stone”, ASTM International, West Conshohocken, PA, 2018.
6.1.10 Negative Side – The dry side of a water-retaining structure where hydrostatic forces push the dampproofing away from the structure.
6.1.11 Non-Vitreous – Describes a material having a % absorption of water by weight greater than or equal to 7%. Non-Vitreous materials are suitable for interior vertical surfaces only but not exterior locations or submerged.
“ASTM C97-18 Standard Test Methods for Absorption and Bulk Specific Gravity of Dimension Stone”, ASTM International, West Conshohocken, PA, 2018.
6.1.12 Permeability – The ability of a given concrete to permit liquids or gases to pass through.
“CT-18 ACI Concrete Terminology”, American Concrete Institute, Farmington Hills, MI, 2018
6.1.13 Positive Side – The wet side of a water-retaining structure where hydrostatic forces push the dampproofing into the structure.
6.1.14 Semi-Vitreous – Describes a material having a % absorption of water by weight of 3% to 7%. Semi-Vitreous materials are suitable for interior locations but not exterior locations or submerged.
“ASTM C97-18 Standard Test Methods for Absorption and Bulk Specific Gravity of Dimension Stone”, ASTM International, West Conshohocken, PA, 2018.
6.1.15 Vapor Retarder – A membrane that impedes the transmission of gas molecules.
“CT-18 ACI Concrete Terminology”, American Concrete Institute, Farmington Hills, MI, 2018
6.1.16 Vitreous – Describes a material having a % absorption of water by weight of 0.5% to 3%. Vitreous materials are suitable for interior or exterior locations but not submerged.
“ASTM C97-18 Standard Test Methods for Absorption and Bulk Specific Gravity of Dimension Stone”, ASTM International, West Conshohocken, PA, 2018.
6.1.17 Waterstop – A thin sheet of metal, rubber, plastic, or other material inserted across a joint to obstruct the seepage of water through the joint.
“CT-18 ACI Concrete Terminology”, American Concrete Institute, Farmington Hills, MI, 2018
6.1.18 Watertight – Impermeable to water except when under hydrostatic pressure sufficient to produce structural discontinuity by rupture.
“CT-18 ACI Concrete Terminology”, American Concrete Institute, Farmington Hills, MI, 2018
6.1.19 w/c – See water-cement ratio.
“CT-18 ACI Concrete Terminology”, American Concrete Institute, Farmington Hills, MI, 2018
6.1.20 w/cm – See water-cementitious materials ratio.
“CT-18 ACI Concrete Terminology”, American Concrete Institute, Farmington Hills, MI, 2018
6.1.21 Water-Cement Ratio – The ratio of the mass of water, exclusive only of that absorbed by the aggregates, to the mass of Portland cement in a cementitious mixture, stated as a decimal and abbreviated as w/c. (See also water-cementitious materials ratio.)
“CT-18 ACI Concrete Terminology”, American Concrete Institute, Farmington Hills, MI, 2018
6.1.22 Water-Cementitious Materials Ratio – The ratio of the mass of water, excluding that absorbed by the aggregate, to the mass of cementitious material in a mixture, stated as a decimal and abbreviated w/cm. (See also water-cement ratio.)
“CT-18 ACI Concrete Terminology”, American Concrete Institute, Farmington Hills, MI, 2018
6.2 Concrete and Shotcrete
6.2.1 The ACI-318 Exposure Category shall be “P – Requiring low permeability”.
“ACI-318 Building Code Requirements for Reinforced Concrete”, Table 4.2.1, American Concrete Institute, Farmington Hills, MI
6.2.2 The ACI-318 Exposure Severity shall be “Required”.
“ACI-318 Building Code Requirements for Reinforced Concrete”, Table 4.2.1, American Concrete Institute, Farmington Hills, MI
6.2.3 The ACI-318 Exposure Class shall be “P1”.
“ACI-318 Building Code Requirements for Reinforced Concrete”, Table 4.2.1, American Concrete Institute, Farmington Hills, MI. This Exposure Class describes a condition where the structure is “In contact with water where low permeability is required.” This describes all watershapes.
6.2.4 The maximum w/cm shall be 0.50 and the minimum fc’ shall be 4,000 psi.
“ACI-318 Building Code Requirements for Reinforced Concrete”, Table 4.3.1 Requirements for Concrete by Exposure Class for Class “P1”, American Concrete Institute, Farmington Hills, MI.
ACI-350 Code Requirements for Environmental Engineering Concrete Structures, Table 4.2.2 further limits the w/cm to 0.45.
6.2.5 For concrete exposed to freezing and thawing cycles the Exposure Category shall be F1, F2, or F3 and the maximum w/cm shall be 0.45 and the minimum fc’ shall be 4,500 psi.
“ACI-318 Building Code Requirements for Reinforced Concrete”, Tables 4.2.1 and 4.3.1, American Concrete Institute, Farmington Hills, MI
ACI-350 Code Requirements for Environmental Engineering Concrete Structures, Table 4.2.2 further limits the w/cm to 0.42.
6.2.6 For concrete exposed to sulfate (SO4) in soil or dissolved sulfate in water the Exposure Category shall be S2 or S3 and the maximum w/cm shall be 0.45 and the minimum fc’ shall be 4,500 psi.
“ACI-318 Building Code Requirements for Reinforced Concrete”, Tables 4.2.1 and 4.3.1, American Concrete Institute, Farmington Hills, MI
ACI-350 Code Requirements for Environmental Engineering Concrete Structures, Table 4.2.2 further limits the w/cm to 0.42.
6.2.7 For concrete exposed to moisture and an external source of chlorides from salt, brackish water, seawater, salt-chlorinators, or spray from these sources the Exposure Category shall be C2 and the maximum w/cm shall be 0.40 and the minimum fc’ shall be 5,000 psi.
“ACI-318 Building Code Requirements for Reinforced Concrete”, Tables 4.2.1 and 4.3.1, American Concrete Institute, Farmington Hills, MI.
Since ACI-318 requires this of concrete exposed to “spray from these sources” which could include “brackish water” it seems reasonable that any salt-chlorinated pool shall be constructed to this standard. This is our recommendation and salt-chlorinators is added to ACI’s description of the condition.
ACI-350 Code Requirements for Environmental Engineering Concrete Structures, Table 4.2.2 also limits the w/cm to 0.40.
6.3 Dampproofing & Tile Installation
6.3.1 For Watertight concrete, shotcrete, or CMU pool, spa, and water feature structures using a bonded mortar bed with ceramic or glass tile, use TCNA’s Detail P601MB-18.
“Handbook for Ceramic, Glass, and Stone Tile Installation”, The Tile Council of North America, Inc. (TCNA), Anderson, SC, 2018.
Some manufacturers publish product-specific versions of the TCNA detail such as Laticrete’s P601, P601A, P601B, P601C, and P603).
6.3.2 For Watertight concrete, shotcrete, or CMU pool, spa, and water feature structures using a thin-bed installation with ceramic or glass tile, use TCNA’s Detail P601TB-18.
This detail shall not be used for competition pools or other structures where strict dimensional criteria is required – use P601MB-18 instead.
The shell must meet 1/8” in 10’ and 1/16” in 1’ finish tolerance and have a concrete surface profile (CSP) of 3 or better. When these tolerances cannot be met, use P601MB-18 instead.
“Handbook for Ceramic, Glass, and Stone Tile Installation”, The Tile Council of North America, Inc. (TCNA), Anderson, SC, 2018.
Also, from page 280: “Shotcrete tanks typically do not meet required substrate tolerances for thin-bed tile installation.”
Some manufacturers publish product-specific versions of the TCNA detail such as Laticrete’s P601D, P602, and P604).
6.3.3 For non-watertight concrete, shotcrete, or CMU pool, spa, and water feature structures using cementitious waterproofing (dampproofing) and a bonded mortar bed with ceramic or glass tile, use TCNA’s Detail P602-18. See also Laticrete P602, P603, and P604.
“Handbook for Ceramic, Glass, and Stone Tile Installation”, The Tile Council of North America, Inc. (TCNA), Anderson, SC, 2018.“Handbook for Ceramic, Glass, and Stone Tile Installation”, The Tile Council of North America, Inc. (TCNA), Anderson, SC, 2018.
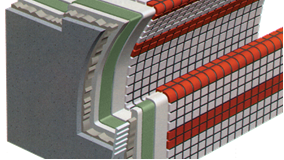
6.4 Protectants and Treatments
6.4.1 Protectants and treatments are highly recommended but should not be considered as stand-alone dampproofing for pools, spas, or water features. Examples of protectants and treatments include colloidal silicates or hydro gels such as:
Aquron CPSP
Miracote MiraPrime Aqua-Blok XL
Xypex C-500, C-1000, or C-2000
6.4.2 Protectants and treatments shall be removed from the surface of the pool, spa, or water feature structure prior to the application of any additional mortars, thinsets, dampproofing, tile, stone, plaster, or other veneers. Pressure washing is the preferred method.
Colloidal silicates densify the concrete and help reduce efflorescence but will not seal or bridge a hairline crack. Therefore, we cannot consider them to be stand-alone dampproofing products.
Because mitigation of efflorescence is important for aesthetics and long-term durability of the structure and finishes we highly recommend using colloidal silicates even when dampproofing membranes are installed.
Colloidal silicates will provide a bond-break between the concrete and applied finishes. For this reason the surface must be free of all applied or integral (e.g., Xypex) products.
6.5 Rigid Cementitious Dampproofing
6.5.1 Rigid cementitious dampproofing should not be used for pools, spas, or water features. Examples of rigid cementitious dampproofing include:
- Sika®-101A
- Sikaseal®-250 Migrating
- Thoroseal
Rigid cementitious dampproofing products are typically single-component dry powders mixed with water. Because they are not flexible they cannot bridge cracks that will develop when the structure deflects under load.
Most tile setting material manufacturers do not include rigid cementitious materials as part of a warrantied system. Some manufacturers of rigid cementitious products specifically state “not recommended for swimming pools”.
6.6 Fluid Applied Elastomeric Dampproofing
6.6.1 Fluid applied elastomeric dampproofing is recommended if all of the following criteria are met:
- Product meets the ANSI A118.10 Standard Specifications for Load Bearing, Bonded, Waterproof Membranes for Thin-set Ceramic Tile and Dimension Stone Installation.
- Applied in a “bath-tub” application where the entire pool, spa, or water feature vessel is coated up above the waterline.
- Not used in a partially submerged application where water could get under the edge and promote delamination (e.g., waterline tile) unless specifically approved by the manufacturer in writing.
- Not used under plaster even if a scratch coat is applied between the fluid applied elastomeric and the plaster.
- Not used in Negative-Side applications.
- Applied per the manufacturer’s instructions over a pressure-washed-clean substrate with an appropriate concrete surface profile (CSP) for the product.
Examples of fluid applied elastomeric dampproofing include:
- Laticrete Hydro Ban®
- Multicoat Mulasticoat®
Fluid applied elastomerics are typically single-component liquids rolled or brushed onto the substrate. They form a very flexible rubber-like membrane that is excellent for crack-isolation under tile but is subject to tearing and delamination when certain forces are applied to it.
For example, if water gets under the membrane the hydrostatic pressure can delaminate the membrane. This can occur in a Negative-Side application or when the product is only partially installed below the water surface and the water can get behind the membrane and push it off the substrate. It is important that the substrate be clean and finished with the appropriate concrete surface profile to promote a good bond and eliminate delamination.
Some manufacturers of fluid applied elastomerics have limits on the size of tile that can be used over the membrane. This is because expansion and contraction could shear the rubber-like material. Cementitious finishes such as plaster can have significant shrinkage that will quickly shear the membrane and delaminate the plaster. For this reason we do not recommend using fluid applied elastomerics under plaster.
6.7 Highly Modified Cementitious Dampproofing
6.7.1 Highly modified cementitious dampproofing is recommended if all of the following criteria are met:
Builder is satisfied that the product’s performance is acceptable (most are not tested to the ANSI A118.10 Standard Specifications for Load Bearing, Bonded, Waterproof Membranes for Thin-set Ceramic Tile and Dimension Stone Installation).
May be used in a partially submerged application.
May be used under plaster if it is protected from the plaster application methods (spiked shoes, for example, can puncture the membrane).
May be used in both Negative-Side and Positive-Side applications.
Applied per the manufacturer’s instructions over a pressure-washed-clean substrate with an appropriate concrete surface profile (CSP) for the product.
Examples of highly modified cementitious dampproofing include:
- Basecrete Flexible Waterproof Bondcoat
- Flexcrete Flexible Concrete Waterproofing
- Miracote MiraFlex Membrane C
Highly modified cementitious dampproofing products are typically Portland-based latex modified dual-component systems rolled or brushed onto the substrate. They form a semi-flexible membrane that is sufficient for crack-isolation under tile.
When using highly modified cementitious dampproofing under plaster, the membrane must be protected from damage by spiked shoes, trowels, pump hoses, etc. Some manufacturers might recommend a scratch coat be applied over the membrane prior to applying a plaster finish.
6.8 Substrate Preparation
6.8.1 The substrate (typically concrete) shall be fully cured and ready to accept subsequent layers of material and all materials in succession must be allowed to cure per the manufacturer’s instructions. All layers shall be compatible with each other and we recommend using a complete system from a single manufacturer if possible.
A common cause of failures is applying products over unprepared non-cured substrates. Keep in mind that if these are indeed dampproofing products they shouldn’t allow moisture out of their substrate just like they shouldn’t allow moisture through the surface.
6.9 Plaster
6.9.1 Plaster is not dampproofing or waterproofing.
“Technical Manual”, National Plasterers Council (NPC), Wauconda, IL, 2016
6.10 Plastics
6.10.1 Exposed plastics shall have U.V. inhibitors.
This delays the material from yellowing.
6.11 Tile Materials
6.11.1 Tile (porcelain, glass, natural stone, etc.) shall be vitreous or impervious when used outdoors in dry locations only and shall be impervious when used in submerged locations.
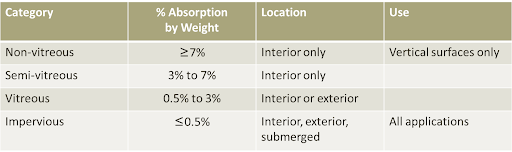
6.11.2 Do not use clay tiles, Saltillo, or Terracotta tiles.
Saltillo and Terracotta have % absorption by weight of 12% to 20% and will not hold up in submerged applications.
6.11.3 Do not use slate stone.
Slate gets “flaky” with sharp edges – especially in submerged applications.
6.11.4 Do not use stone that contains iron or other materials that will bleed or stain.
6.11.5 Tile shall be slip resistant with a coefficient of friction (μ) of 0.42 min.
Model Aquatic Health Code (MAHC), U.S. Department of Health and Human Services, Centers for Disease Control and Prevention, Atlanta, GA, 2018.
6.11.6 Glass tile is suitable for use in pools, spas, and water features if all of the following criteria are met:
- Glass tile when used must meet or exceed testing per ANSI 137.2-the glass tile standard.
- Manufacturer states in writing the tile is suitable for usage in a submerged/wet-dry environment such as pools/spas.
The tile uses a paper or polymer facing and not a mesh mounted. - The tile is fully bonded with a thin-set mortar approved for glass tile to reduce the potential for failure.
- The tile has adequate movement joints per TCNA EJ-171 guidelines to prevent failure due to movement, expansion, or contraction.
- No sharp edges are exposed where they might injure an occupant.
Additional Considerations:
- The tile has been annealed to remove most internal stresses.
- Be very careful if considering larger format glass tile. The larger size may not allow for enough movement to mitigate thermal expansion and contraction issues. Check with manufacturer for specific size restrictions.
- Be very careful if considering recycled glass tile because they might include contaminants that might contribute to cracking – especially in thermal-shock conditions or freeze thaw conditions.
“ANSI 137.2-2018 American National Standard Specifications for Glass Tile”, The Tile Council of North America, Inc. (TCNA), Anderson, SC, 2018.
“Handbook for Ceramic, Glass, and Stone Tile Installation”, The Tile Council of North America, Inc. (TCNA), Anderson, SC, 2018.
“American National Standard Specifications for the Installation of Ceramic Tile”, Materials and Installation Standards, The Tile Council of North America, Inc. (TCNA), Anderson, SC, 2018.
“Handbook for Ceramic, Glass, and Stone Tile Installation”, The Tile Council of North America, Inc. (TCNA), Anderson, SC, 2018.
Many failures of glass tile originate with improper dampproofing, incorrect setting methods and materials, and a lack of flexible movement joints.
Mesh mounted tile is prone to delaminate due to:
- Glue adhering tile to mesh is water-soluble.
- Swelling of the fiber mesh.
- Inadequate bond of the tile because the mesh interferes with the thinset connecting to the glass.
6.12 Metals
6.12.1 Stainless steel shall be Type 304 or Type 316 (preferred) and shall not contain nickel pig iron (NPI). If using salt chlorination then Type 316 is required and all welds should be passivated per ASTM A967 Standard Specification for Chemical Passivation Treatments for Stainless Steel Parts.
Nickel pig iron (NPI) is a low grade ferronickel used as an inexpensive alternative to pure nickel for the production of stainless steel. It does not hold up as well.